One of the five reasons why engaged and committed employees leave is because they are unable to work efficiently. The following real-life example helps shed light on an all too common issue in the logistics industry.
Efficiency in logistics companies: The case of Henry the forklift driver
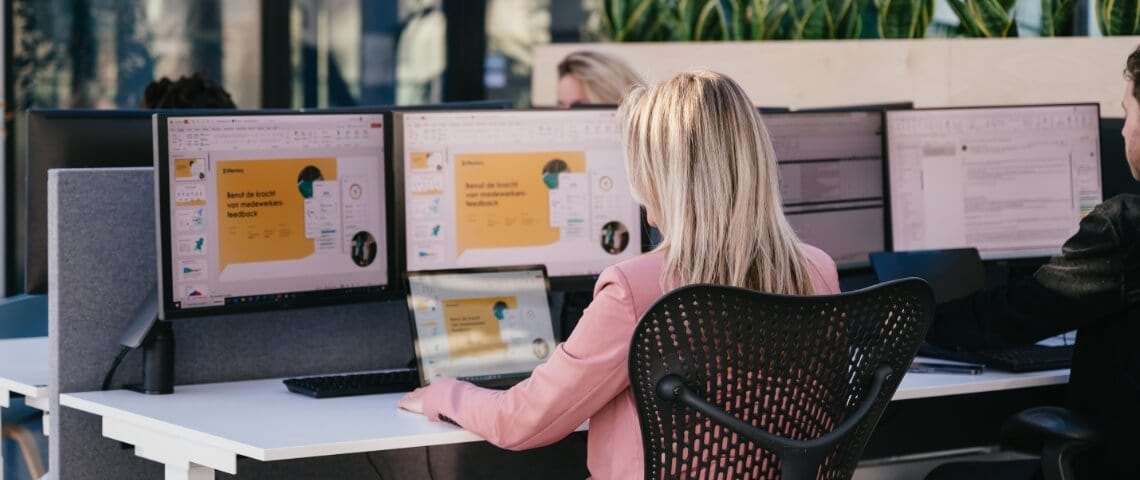
Henry vs. the battery
Henry is a forklift driver at a logistics company. Henry loves his job, and loves helping deliver packages to clients on time. One day he goes into work and discovers that there is a fault in the forklift battery, and that the forklift is unable to run at full power. Henry reports the issue to his immediate manager, who asks him to fill in a form about the issue. Once Henry fills in the form, his immediate manager informs him he has to forward it to the maintenance and purchasing department.
Henry vs. the forms
The maintenance and purchasing department inform Henry that orders for new batteries are placed once a month, and if Henry hurries and gets the paper work in before 12pm, he can make this month’s order. Unfortunately, as the expense is above €500 Henry now has to fill in a new form to be approved by Finance. Henry is eager to join this month’s order and so he calls to follow up the form he sent to Finance. As soon as someone picks up the phone, Henry is told that his form has joined the waiting list and as it is not a priority, it is unlikely that he will have approval sent back to him before the 12pm order deadline. Imagine the frustration that Henry now feels, and just how much harder Henry’s job has become. Not only has Henry spent the whole day trying to solve the issue, he now has to drive his forklift at half
capacity for the whole month.
Global Employee Engagement Index™
Discover the Global Employee Engagement Index™ 2025 for key insights on driving employee engagement, improving performance, and enhancing team dynamics.
DownloadTrust
Understandably, rules are in place to control expenses. However, if you want to increase efficiency you need to give up some degree of control. To do this successfully, there needs to be trust within the organisation. Managers need to trust employees to do their jobs, and adopt a management style that reflects this. The alternative is managing according to control, which as Henry’s case illustrates, creates a very inefficient working environment.
For poor old Henry his life would be much easier if he was trusted to take care of his underperforming forklift. If one instance of approval were sufficient (instead of three), his work would become much more efficient. Imagine the impact on Henry if employees were able to order equipment up to a value of, say, €1000, without manager approval.
Although this is a specific example, it holds a general value. Virtually every organisation has a story that resembles Henry’s. By trusting employees and listening to their input on how to improve conditions on the work floor, organisations increase efficiency as well as engagement.
How to gather feedback from your employees
The definitive checklist for creating your employee engagement survey.
Download